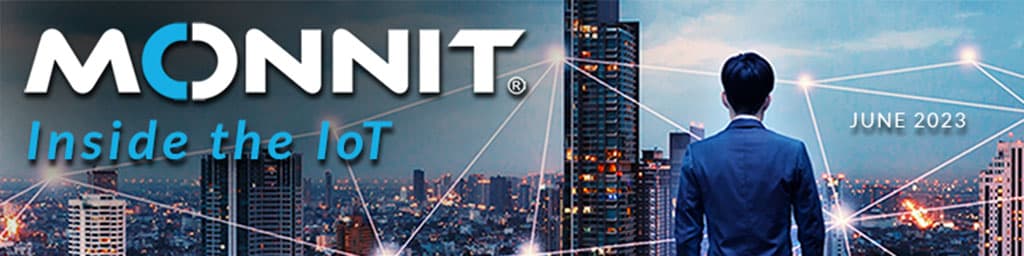
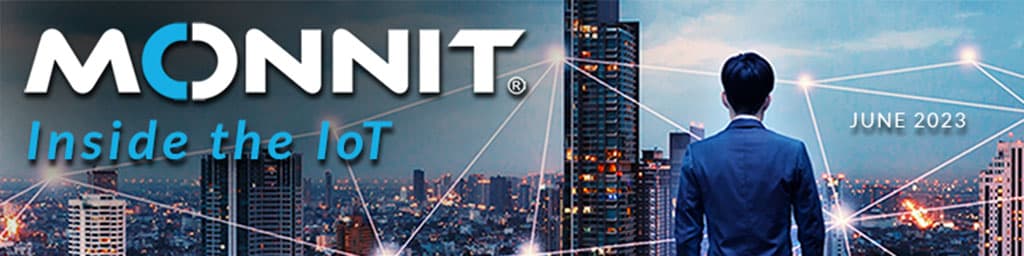
Internet of Things Intersection
Where Hazardous Environments and Intrinsically Safe IIoT Sensors Meet
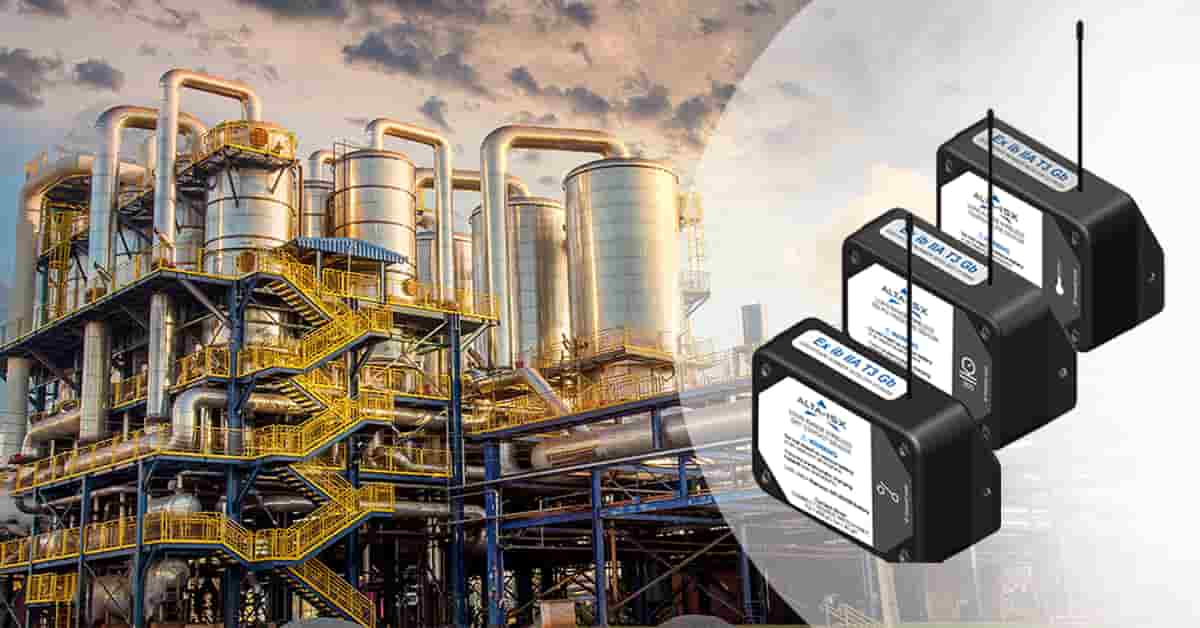
There are major advantages of using intrinsically safe sensors in hazardous environments; none are more significant than life-saving. So if you need to monitor industrial processes, sensors connected to the Industrial Internet of Things (IIoT) must possess intrinsic barriers to ensure they don’t create a spark or overheat, igniting surrounding volatile gases, powders, and liquids.
This article in Tech Briefs by Monnit Electrical Engineer Stephen Preston goes behind the scenes to show how we created our intrinsically safe hazardous duty ALTA-ISX® Sensors.
Please take a few minutes to read the article’s introduction below. For the full article, click the links.
How to Engineer Intrinsically Safe Hazardous Duty Wireless Sensors
An apparatus such as a wireless sensor used in a hazardous location must be designed and certified to meet the required safety standards. Those standards are amplified when the environment and work already deemed inherently hazardous duty is done in areas where explosive (Ex) atmospheres are anywhere from always to only rarely present.
Risks from Explosive Atmospheres are in Many Industries
It’s easy to consider explosive atmospheres in the oil and gas industry as hazardous locations for electrical equipment—at petrochemical and refining facilities, field and offshore drilling operations, and gas stations. But explosive atmospheres with flammable and combustible gases, vapors, dust, powders, and fibers can be present in other industrial applications—such as chemical production, pharmaceutical and cosmetics manufacturing, food processing, power generation, mining, construction, and architectural woodworking.
By law and good sense, everything and everyone must be safeguarded and certified according to the safety standards for these hazardous locations. What’s the risk? One tiny spark or overheated device could ignite an explosion, causing damage, injury, or even loss of life.
Engineers Make Critical Design Decisions
For operations in explosive or potentially explosive atmospheres, engineers must ensure each process, system, and apparatus meets or exceeds safety regulations from design to production to installation and operation. Engineers can use several protection methods against explosive atmospheres to create safe hazardous-duty sensors.
Vertical Market Focus
Make Manufacturing Hum with Connected Things
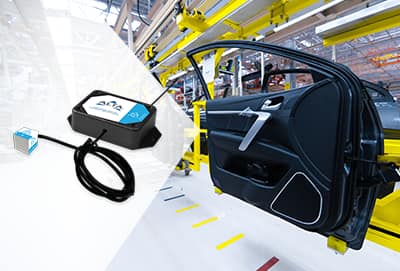
The Industrial Internet of Things (IIoT) continues to transform manufacturing. With a network of sensors and meters to instantly collect critical production data, you can turn this data into valuable, actionable insights to boost your manufacturing operations.
This will help you increase uptime and overall equipment effectiveness (OEE)—critical drivers of the manufacturing industry’s success and our economy. The ability to predict machine performance and schedule maintenance using IoT sensors and cloud-based software can keep factories running strong and seamlessly.
See how a manufacturer boosted line productivity, optimized predictive maintenance, and reduced machine downtime.
Monnit Events
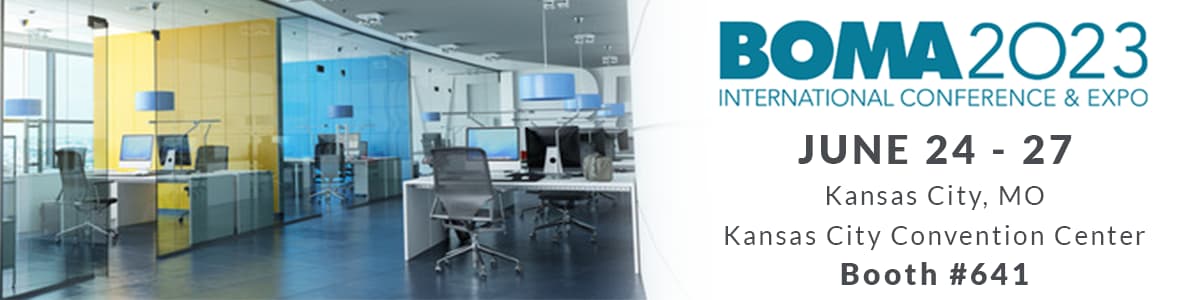
Monnit Korea Events
.jpg)
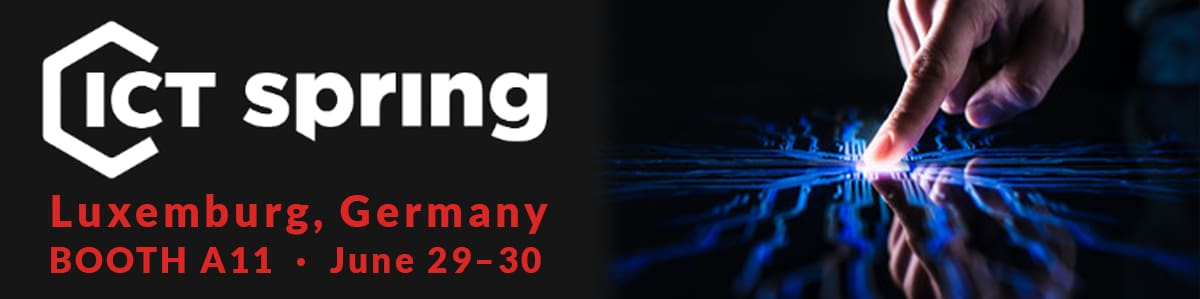
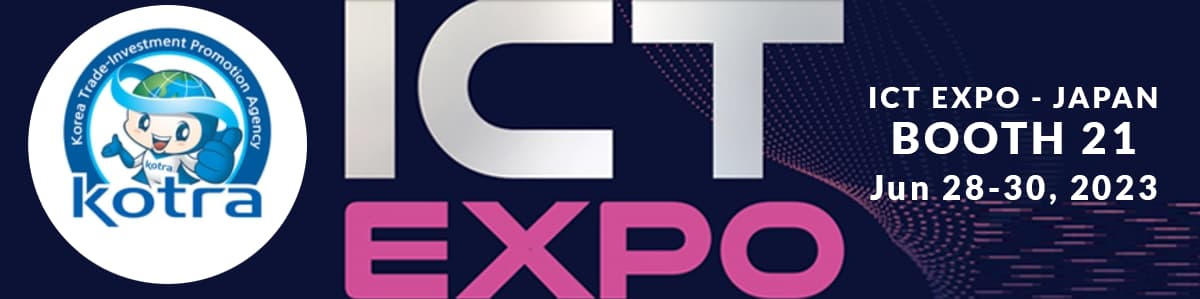
IoT Insights
The Benefits of Integrating the IoT and AI into Asset Management
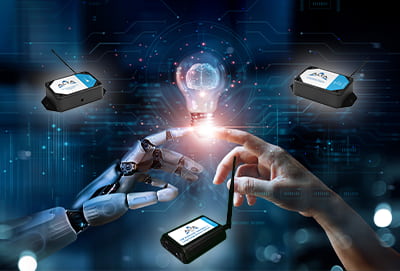
When IoT and AI technologies work in tandem, they can help you better visualize, plan, and maintain your assets across your organization. The benefits of adding an IoT and AI platform to your asset management program include increased automation, real-time asset tracking, data-driven decision-making, and streamlined tasks.
This short article by Terence West summarizes how the growth and adoption of IoT and AI technologies increase the potential for predictive maintenance to transform asset management across various industries. Read the beginning below and click a link to review the full article.
Predictive Maintenance: Revolutionalizing Asset Management with IoT and AI
Predictive maintenance is revolutionizing asset management by leveraging the power of the Internet of Things (IoT) and artificial intelligence (AI). By integrating these cutting-edge technologies, businesses can now monitor the health of their assets in real-time, anticipate potential failures, and schedule maintenance activities accordingly. This not only reduces downtime and operational costs but also extends the life of equipment and enhances overall productivity.
The Internet of Things has transformed the way we interact with the world around us. By connecting everyday objects to the internet, we can now gather data, analyze it, and use it to make informed decisions. This has opened up a plethora of opportunities for businesses to optimize their operations and gain a competitive edge. One such opportunity is the implementation of predictive maintenance strategies.
Predictive maintenance is a proactive approach to asset management that uses data analysis to identify potential equipment failures before they occur. By continuously monitoring the performance of machinery and analyzing the data collected, businesses can detect anomalies and signs of wear and tear, allowing them to address issues before they escalate into costly failures. This is where IoT and AI come into play.
Read the rest of the article.Free IoT Consultation
.jpg)
IoT Webinars
.jpg)
All trademarks are property of respective owners. Copyright © Monnit Corp. All rights reserved.
Monnit Corporation | 801-561-5555 | monnit.com